AccountingSuite utilizes a stringent inventory management system, meaning that if an item is not available in stock, it cannot be sold. It is essential to comprehend how this inventory system operates to prevent scenarios where “Insufficient inventory” error alerts may appear. This document will attempt to explain how quantity on hand counts are changed in AccountingSuite and how you can troubleshoot inventory issues.
Only Product items in AccountingSuite are inventoried. Service items are not inventoried.
Documents that Have an Affect on Quantity on Hand #
Item Receipts – when Receiving Items, Saving the Item Receipt will increase the quantity of the quantity on hand of the items on the item receipt at the locations specified on the Ship To* field on the line.

If you do not use Item Receipts, this change will happen when saving the Bill
Bills – when saving a bill, quantity on hand will increase for items on the bill at the locations specified on the Ship To* field on the line.

If you use Item Receipts, this change will happen when saving the Item Receipt. In this case, the Bill has NO affect on the quantity on hand.
Shipments – when shipping orders, the quantity on hand will decrease for items on the shipment at the location* specified in the Ship From field on the line.

If you do not use Shipments, this change will happen when saving the Sales Invoice.
Sales Invoices – when saving a Sales Invoice, the quantity on hand will decrease for items on the invoice at the location* specified on the Ship From field on the line.

If you use Shipments, this change will happen when the Shipment is saved.
Warehouse Transfers – when saving a Warehouse Transfer, inventory quantity on hand will decrease at the location specified in the From field and increase in the To field for the items on the Warehouse Transfer.
Inventory Adjustments – the quantity on hand with increase with a positive number in the adjustment field or decrease with a negative number.
Assembly Builds – the quantity on hand will increase by the quantity to make indicated on the Assembly Build and the quantity on hand will decrease for all of the items on the bill of materials by the quantities specified on the lines.
Disassemblies – the quantity on hand will decrease by the quantity to disassemble indicated on the Disassembly and the quantity on hand will increase for all of the items on the bill of materials by the quantities specified on the lines.
Troubleshooting Inventory Problems #
Two things that cause 90% of inventory problems:
- Incorrect date on the Item Receipts / Shipments.and
- Incorrect Ship from and Ship To locations on the Item Receipts / Shipments.
Incorrect Dates on Item Receipts / Shipments or Other Documents #
Order of documentation is very important. Please record the documents in the order that they happened in real life. Here are some things to check:
- Does your Purchase Order have an later date than your Item Receipt(or Bill)? It is not possible to receive something before you order it. Purchase Order date must be before Item Receipt date.
- Does your Shipment (or Sales Invoice) have an earlier date that your Item Receipt? It is not possible to ship inventory that you have not yet received. Shipment date must come after Item Receipt date.
Here is the order in which documents should be created for several different scenarios:
Sales Order, Purchase Order, Item Receipt, Shipment (the following group of documents must come after the previous list but order is not important: Sales Invoice, Cash Receipt, Bill, Bill Payment) -or- Purchase Order, Item Receipt, Sales Order, Shipment (Sales Invoice, Cash Receipt, Bill, Bill Payment)
Sales Order, Purchase Order, Bill, Sales Invoice. (Cash Receipt and Bill Payment must come after the previous list but order is not important) -or- Purchase Order, Bill, Sales Order, Sales Invoice (Bill Payment, Cash Receipt)
Purchase Order, Item Receipt, Cash Sale, Bill, Bill Payment
Item Receipt, Sales Invoice

The important thing to note is the you MUST receive the inventory BEFORE you ship or invoice it.
Incorrect Locations #
Ship from and Ship to locations are very important on the documents that affect inventory. Look at the LINE and NOT the header when determining which location an item was received into or shipped from.
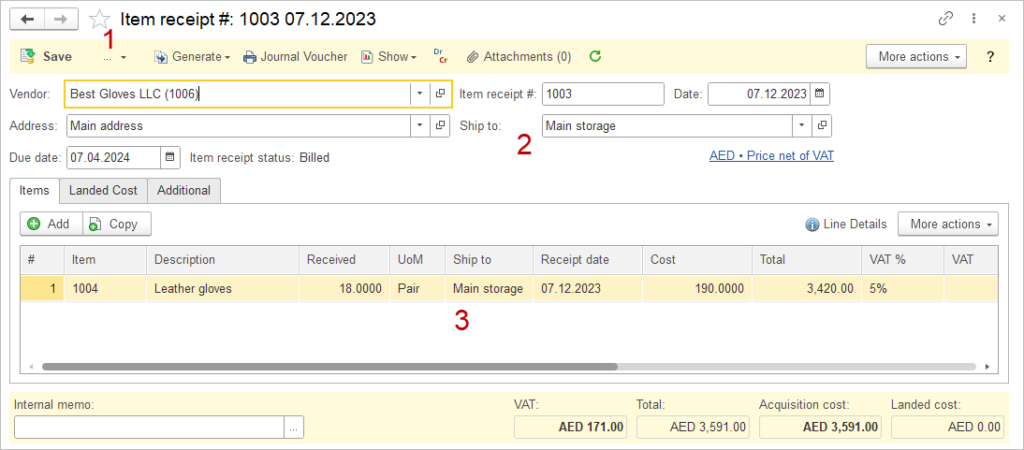
- Document that affects inventory
- Only sets default for lines
- The location where inventory was received
Other Things to Check/Try #
- Run a Quantity on Hand by Location Report. Note quantities on hand that don’t look correct.
- Run an Item Activity Report which will show you the times when quantity on hand was changed for an item and which document changed it.
- Ensure all documents that affect inventory have been posted. There will be a green checkmark icon next to the document in the list if it has been posted.
- On the Purchase Order, go to More Actions, Show Columns. This will show you counts of Ordered, Shipped (or Received) and Invoiced (or Billed).
- Resave all documents in the order that they were created to ensure they are all posted correctly.
- Review all locations on documents that affect inventory to ensure they were received into and shipped from the correct locations.
If you do not have multi-location features enabled, you will not have a Ship from or Ship to field on the line as there is only one location, your default warehouse.
If you do not have Multi-location features enabled, you will not see the Warehouse Transfer document in your account.